|
|
NanoAutomation - A Design Philosophy to Achieve Nanometer Precision Faster
|
|
While nanopositioning systems are not quite commodities, yet, they have made the transition from exotic "toys" for research to well accepted tools for manufacturing, test and inspection in all high-tech industries.
When PI engineers designed nanopositioning systems with higher and higher precision they learned that in today's demanding applications better resolution alone does not solve the customer's problem.
NanoAutomation® takes nanopositioning to the next level. It defines solutions that perform exceptionally well in real world applications improving speed, stability, throughput and quality. NanoAutomation® means achieving nanometer and sub-nanometer level precision faster, reapeatedly.
This philosophy optimizes all parts of the nanopositioning system with respect to the individual application.
Read the NanoAutomation Blog
NanoAutomation® is the result of thousands of nanopositioning solutions designed in the last 40 years.
|
|
Serial Kinematics vs. Parallel Kinematics Piezo Flexure Nanopositioning Systems
|
|
| | | | |
Stacked Serial Kinematics XY Flexure
Nanopositioning System
-
Simple Design, but:
-
Slower response (lower stage
carries inertial mass of upper stage)
-
Non-symmetric resonant frequencies
(lower stage is slower than upper stage, requires different servo settings).
-
Orthogonality is mounting-angle
dependant.
-
Runout in XY cannot be monitored/ compensated
by the sensor in other axis.
|
|
Nested Serial Kinematics XY Flexure
Nanopositioning System
-
Thinner and better response than Stacked Serial Kinematics, but no other advantages.
|
|
Parallel Kinematics
Flexure Nanopositioning System (Three-axis stage shown)
- Active Trajectory Control: All motion is kept inside the servo loop.
-
Same ultra-low inertia for
X and Y motion, providing higher responsiveness and axis-independent performance.
-
Excellent, mounting independent
orthogonality.
-
Additional rotation axis (Theta
Z) feasible with 3 actuators / sensors and digital controller.
|
Advanced Digital Controllers and Control Algorithms |
|
Nanopositioning systems are mostly used in dynamic mode (scanning, tracking etc.) Static resolution figures become meaningless here. The key performance parameters of the positioning system and the surrounding components are tracking error, following error, dynamic linearity and stability, responsiveness, vibration and settling time. PI offers a number of a advanced digital controllers and algorithms that eliminate tracking errors, self-generated vibrations and vastly improve dynamic performance and throughput.
Click Here for Information on Faster Settling.
See How DDL Improves Scanning Linearity up to 1000-Fold.
An Example of an Ultra-Fast Positioning Controller in a Track Following Servo Disk Drive Application.
| | 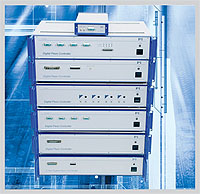 Variety of digital piezo controllers.
| | 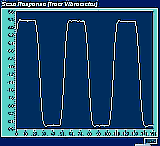 Signal pre-shaping eliminates self-generated vibration, increases throughput, scanning speed, and accuracy.
|
HyperBit
|
|
Benefits: Higher Resolution at no Additional Cost, Higher Stability. HyperBit, a newly-patented technology (US Patent# 6,950,050), takes advantage of the fact that as fast as piezoelectric actuators can respond, DACs are even faster. By performing high-speed time-domain modulation of the least-significant bits of the DAC at a rate at which the piezo system cannot respond to, many additional bits of positioning resolution can be achieved with no loss in bandwidth or stability.
More on HyperBit
| | 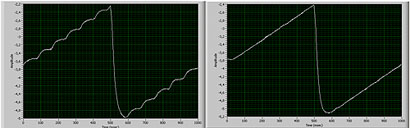 High-resolution interferometry of raster scan, of amplitude ~10•LSB.
(Left) Bitwise step activity of DAC can be seen. (Right) HyperBit adds additional resolution, improving the dynamic accuracy of the scan
|
Two Plate Capacitive Position Sensors with Ultra-Low Noise, Auto-Linearization Electronics |
|
Benefits: Direct output metrology, measures position directly where motion occurs. Non contact, no friction, highest resolution and lin- earity of any commercially available sensor. UHV compatible.
More on Capacitive Position Sensors and Nanopositioning Stages.
| | 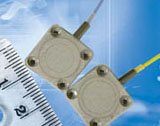 Two plate capacitance sensors. | | 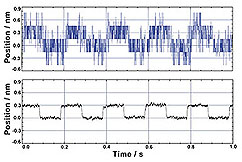 Piezo nanopositioning stage making 0.3 nm steps, measured with PI capacitive sensor (lower curve) and with a laser interferometer. The capacitive sensor provides significantly higher resolution than the interferometer. |
Piezo Nanopositioning Systems with AutoCalibrate Function
|
|
Benefits: Improves peerformance. Reduces downtime. The calibration data is stored right in the connector of the Nanopositioning system itself. Controller and nanomechanism can be interchanged for upgrades or maintenance at any time.
Read More about Advanced Control Algorithms
| | 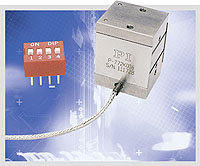 Miniature Piezo Nanopositioning / scan- ning stage with AutoCalibrate feature. | | 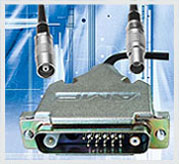 PI Piezo systems are equipped with high performance connectors for ultra-low noise, and EMI compliance. |
High Performance Piezo Ceramics
|
|
Benefits: Longer lifetime under extreme conditions, higher dynamic performance, UHV compatible.
PI is the only Nanopositioning Systems manufacturer with the capability to develop and produce Piezo ceramics. The patented PICMA® Piezo Actuators are the only ceramic encapsulated piezo multilayer actuators.
Learn More about PICMA® Piezo Actuators.
Piezo Acutators on Mars Rover
| | 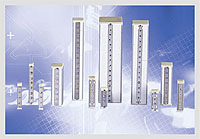 PICMA® multilayer piezo actuators are currently available with cross-sections of 2 x 3, 3 x 3, 5 x 5, 7 x 7 and 10 x 10 mm. | |
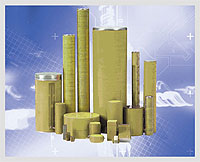 Variety of standard and custom PICA™-Stack piezo actuators, for high force applications. |
PILine® High-Speed Ultra Sonic Drives |
PILine® motors are based on a novel, patented ultrasonic drive developed by PI. At the heart of the system is a piezoceramic plate which is excited to produce high-frequency eigenmode oscillations. A friction tip attached to the plate moves along an inclined linear path at the eigenmode frequency. Through its contact with the friction bar, it drives the moving part of the mechanics forward or backwards. With each oscillatory cycle, the mechanics executes a step of a few nanometers; the macroscopic result is smooth motion with a virtually unlimited travel range.
More on PILine® Miniature Ultrasonic Piezomotors
|
| 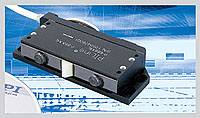 Ultrasonic piezo motors can provide forces to 50N.
| | 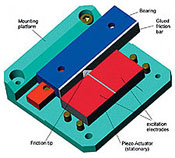 Principle design of a PILine® ultrasonic piezomotor-driven translation stage. |
|
|
NanoAutomation®: Achieve Nano-Precision Faster |
|
|
© 1996-2006 PI (Physik Instrumente) L.P. All Rights Reserved.
Specifications subject to change without notice. |
|